Kegagalan komponen adalah keniscayaan untuk mesin otomotif, peralatan industri berat, atau bahkan perangkat elektronik sederhana, setiap bagian memiliki batas umur dan kondisi operasional.
Ketika sebuah komponen mesin gagal, dampaknya bisa bervariasi dari gangguan kecil hingga bencana besar yang melibatkan kerugian finansial, kerusakan properti, bahkan hilangnya nyawa. Oleh karena itu, analisis kegagalan (failure analysis) menjadi disiplin ilmu yang sangat penting dalam rekayasa.
Analisis kegagalan adalah proses investigasi sistematis untuk menentukan penyebab akar (root cause) dari kegagalan suatu komponen atau sistem. Tujuannya bukan hanya untuk memperbaiki masalah yang ada, tetapi juga untuk mencegah terulangnya kejadian serupa di masa mendatang dengan mempelajari pelajaran dari insiden tersebut.
Mengapa Analisis Kegagalan itu Krusial?
- Peningkatan Keamanan: Mengidentifikasi penyebab kegagalan membantu mencegah insiden serupa yang dapat membahayakan keselamatan manusia.
- Penghematan Biaya: Mencegah kegagalan berulang mengurangi biaya perbaikan, penggantian, dan waktu henti produksi (downtime) yang mahal.
- Peningkatan Keandalan Produk: Memahami bagaimana dan mengapa komponen gagal memungkinkan desainer dan produsen untuk meningkatkan kualitas dan umur pakai produk mereka.
- Perbaikan Desain dan Manufaktur: Memberikan feedback berharga kepada tim desain dan manufaktur untuk melakukan koreksi dan optimasi.
- Klaim Hukum dan Asuransi: Menyediakan bukti teknis yang kuat dalam kasus litigasi atau klaim asuransi.
Langkah-langkah dalam Proses Analisis Kegagalan
Analisis kegagalan adalah proses multidisiplin yang melibatkan beberapa langkah kunci:
1. Pengumpulan Informasi Awal dan Latar Belakang
Langkah pertama adalah mengumpulkan sebanyak mungkin informasi tentang kegagalan:
- Detail Operasional: Kapan, di mana, dan bagaimana kegagalan terjadi? Suhu operasi, beban, kecepatan, durasi operasi sebelum kegagalan.
- Riwayat Komponen: Umur komponen, riwayat perawatan, perbaikan sebelumnya, perubahan desain, dan bahan yang digunakan.
- Lingkungan Operasi: Apakah ada faktor korosif, kelembaban ekstrem, atau suhu berfluktuasi?
- Gambar dan Video: Foto dan video kondisi komponen sebelum dan sesaat setelah kegagalan sangat berharga.
- Kesaksian Operator/Saksi: Wawancara dengan orang-orang yang terlibat langsung.
2. Pemeriksaan Visual dan Dokumentasi Awal
- Pembersihan: Bersihkan komponen dengan hati-hati untuk menghilangkan kontaminan, tetapi jangan sampai merusak bukti penting.
- Makroskopik: Periksa komponen secara visual dengan mata telanjang atau dengan kaca pembesar. Cari tanda-tanda retakan, deformasi, perubahan warna, keausan, korosi, atau pola patahan.
- Fotografi: Ambil foto berkualitas tinggi dari berbagai sudut, termasuk foto close-up dari area yang gagal. Dokumentasikan semua temuan secara cermat.
3. Pengujian Non-Destruktif (NDT)
Metode NDT digunakan untuk mendapatkan informasi tanpa merusak komponen lebih lanjut:
- Inspeksi Partikel Magnetik (MPI) / Dye Penetrant Inspection (DPI): Untuk mendeteksi retakan permukaan.
- Ultrasonic Testing (UT): Untuk mendeteksi cacat internal.
- Radiographic Testing (RT): Menggunakan sinar-X atau gamma untuk melihat cacat internal.
- Eddy Current Testing (ECT): Untuk mendeteksi retakan permukaan pada material konduktif.
4. Pengujian Destruktif dan Analisis Material
Jika diperlukan, bagian dari komponen yang gagal akan diambil untuk pengujian lebih lanjut yang merusak sampel.
- Analisis Komposisi Kimia: Menentukan elemen-elemen penyusun material untuk memastikan kesesuaian dengan spesifikasi desain. Metode: Spektrometri Emisi Optik (OES), X-ray Fluorescence (XRF), EDS (Energy-dispersive X-ray spectroscopy) pada SEM.
- Uji Kekerasan (Hardness Testing): Mengukur kekerasan permukaan dan inti material untuk memeriksa apakah perlakuan panas sudah tepat. Metode: Rockwell, Vickers, Brinell.
- Uji Tarik (Tensile Testing): Menentukan sifat mekanis dasar seperti kekuatan luluh (yield strength), kekuatan tarik (tensile strength), dan keuletan (ductility).
- Uji Impak (Impact Testing): Mengukur ketahanan material terhadap beban kejut (misalnya, Charpy atau Izod test).
- Mikroskop Optik (Optical Microscopy): Pemeriksaan struktur mikro material setelah etching untuk melihat ukuran butir, fase material, atau cacat mikro.
- Scanning Electron Microscopy (SEM) dan Fractography: Ini sangat penting. SEM digunakan untuk memeriksa permukaan patahan pada perbesaran tinggi. Fraktografi adalah studi pola patahan untuk menentukan mekanisme kegagalan (misalnya, fatigue, brittle fracture, ductile fracture, stress corrosion cracking).
5. Analisis dan Interpretasi Data
Pada tahap ini, semua data yang terkumpul (dari informasi awal hingga hasil pengujian laboratorium) dianalisis untuk membentuk hipotesis tentang penyebab kegagalan.
- Identifikasi Modus Kegagalan: Menentukan bagaimana komponen tersebut gagal (misalnya, patah, aus, korosi, deformasi plastis).
- Identifikasi Mekanisme Kegagalan: Menjelaskan proses fisik yang menyebabkan kegagalan (misalnya, retak lelah, korosi celah, mulur/creep, overload).
- Identifikasi Akar Penyebab (Root Cause): Ini adalah tujuan utama. Mengapa mekanisme kegagalan tersebut terjadi? Apakah karena cacat material, desain yang buruk, proses manufaktur yang salah, perakitan yang tidak tepat, penggunaan di luar spesifikasi, atau perawatan yang tidak memadai?
6. Kesimpulan dan Rekomendasi
- Menyusun Laporan: Menyajikan semua temuan, analisis, dan kesimpulan secara sistematis dalam laporan tertulis.
- Rekomendasi: Berikan rekomendasi konkret untuk mencegah terulangnya kegagalan. Ini bisa berupa perubahan desain, spesifikasi material, proses manufaktur, prosedur perakitan, jadwal perawatan, atau pelatihan operator.
Jenis-Jenis Kegagalan Komponen Mesin yang Umum
Memahami berbagai jenis kegagalan membantu dalam mengarahkan analisis:
- Kegagalan Lelah (Fatigue Failure): Patahan yang terjadi akibat beban siklik berulang (misalnya, putaran poros) bahkan jika tegangan maksimum jauh di bawah kekuatan luluh material. Ditandai dengan pola "garis pantai" (beach marks) pada permukaan patahan.
- Kegagalan Ulet (Ductile Fracture): Patahan yang disertai deformasi plastis yang signifikan sebelum patah. Permukaan patahan terlihat berserabut atau kasar ("cup and cone"). Terjadi akibat beban statis yang melebihi kekuatan tarik.
- Kegagalan Getas (Brittle Fracture): Patahan tanpa deformasi plastis yang signifikan. Terjadi tiba-tiba dan cepat, seringkali pada material yang rapuh atau pada suhu rendah. Permukaan patahan terlihat halus, berbutir, atau cleavage.
- Keausan (Wear): Kehilangan material dari permukaan akibat kontak dan gerakan relatif. Jenis:
- Abrasive Wear: Akibat partikel keras yang mengikis permukaan.
- Adhesive Wear: Akibat perpindahan material antar permukaan yang bersentuhan.
- Erosive Wear: Akibat partikel atau fluida yang mengikis permukaan.
- Fretting Wear: Keausan pada permukaan yang mengalami gerakan osilasi kecil.
- Korosi (Corrosion): Deteriorasi material akibat reaksi kimia atau elektrokimia dengan lingkungannya.
- Korosi Umum: Serangan merata di seluruh permukaan.
- Korosi Lubang (Pitting Corrosion): Lubang kecil yang terbentuk di permukaan.
- Korosi Celah (Crevice Corrosion): Korosi di celah sempit.
- Stress Corrosion Cracking (SCC): Retakan yang terjadi akibat kombinasi tegangan tarik dan lingkungan korosif.
- Mulur (Creep): Deformasi plastis yang bergantung pada waktu di bawah tegangan konstan pada suhu tinggi.
- Deformasi Plastis/Yielding: Perubahan bentuk permanen yang terjadi ketika tegangan melebihi kekuatan luluh material, tanpa terjadi patah.
- Overload: Kegagalan yang terjadi ketika beban yang diterapkan melebihi kapasitas desain material atau komponen.
Contoh Studi Kasus Singkat
Kasus: Patahan pada poros gearbox di sebuah pabrik semen.
Pengumpulan Informasi Awal: Poros beroperasi terus-menerus. Kegagalan terjadi setelah beberapa tahun operasi. Ada laporan tentang getaran abnormal sebelum kegagalan.
Pemeriksaan Visual: Permukaan patahan menunjukkan area halus dan mengkilap yang menyebar dari satu titik di dekat alur pasak (keyway), diikuti oleh area kasar.
Pengujian Mikroskopis (SEM dan Fraktografi):
- Area halus menunjukkan garis pantai (beach marks) yang jelas, mengindikasikan kegagalan lelah (fatigue failure).
- Titik awal retakan (crack initiation) terlokalisasi di dasar alur pasak.
- Area kasar adalah zona patahan akhir (final fracture zone).
Analisis: Pola garis pantai dan titik inisiasi di alur pasak yang merupakan konsentrasi tegangan khas menunjukkan bahwa poros gagal karena kelelahan. Alur pasak, meskipun penting untuk transmisi torsi, secara inheren menciptakan konsentrasi tegangan yang tinggi, terutama di sudut-sudut tajamnya. Getaran abnormal sebelumnya juga mendukung teori kelelahan.
Rekomendasi:
- Modifikasi Desain Alur Pasak: Membulatkan sudut alur pasak (fillet radius) untuk mengurangi konsentrasi tegangan.
- Pemilihan Material: Pertimbangkan material dengan ketahanan lelah yang lebih tinggi atau perlakuan panas permukaan (misalnya, shot peening) untuk meningkatkan ketahanan lelah di area kritis.
- Inspeksi Rutin: Lakukan inspeksi NDT secara berkala (misalnya, MPI) di area alur pasak pada poros serupa yang masih beroperasi.
- Kontrol Getaran: Selidiki penyebab getaran abnormal pada gearbox untuk mengurangi beban siklik pada poros.
Analisis Kegagalan
Analisis kegagalan adalah tulang punggung keandalan dan keamanan dalam industri rekayasa. Ini bukan sekadar reaksi terhadap masalah, tetapi juga alat proaktif untuk pembelajaran dan peningkatan berkelanjutan. Dengan mengikuti metodologi sistematis, memanfaatkan berbagai teknik pengujian canggih, dan menerapkan interpretasi yang cermat, insinyur dapat mengungkap misteri di balik kegagalan komponen mesin, memberikan wawasan berharga, dan memastikan bahwa kesalahan yang sama tidak akan terulang, sehingga menghasilkan produk yang lebih kuat, lebih aman, dan lebih efisien.
0 Komentar
Artikel Terkait
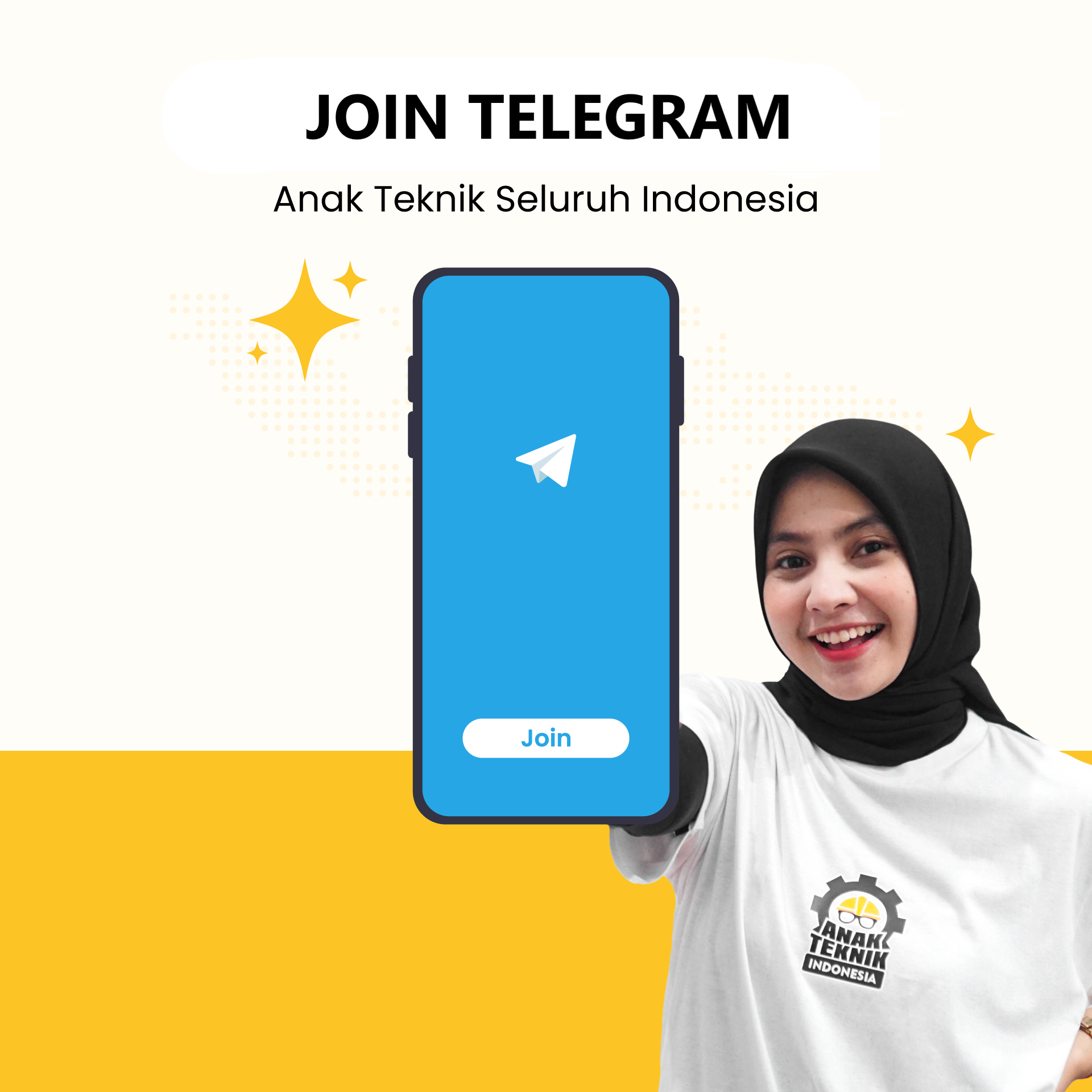