Electrical Discharge Machining (EDM), atau dikenal juga sebagai spark machining, spark eroding, atau wire erosion, adalah proses manufaktur non-konvensional yang revolusioner.
Metode ini menggunakan percikan listrik terkontrol untuk menghilangkan material dari benda kerja. EDM sangat vital dalam memproses material keras atau material dengan geometri kompleks yang sulit atau tidak mungkin dikerjakan dengan metode permesinan tradisional (seperti milling atau turning).
1. Prinsip Kerja EDM
EDM bekerja berdasarkan prinsip erosi material akibat percikan listrik yang berulang dan terkontrol. Berikut adalah komponen dan proses utamanya:
- Elektroda (Tool Electrode): Ini adalah pahat non-kontak yang terbuat dari material konduktif listrik (umumnya grafit atau tembaga). Elektroda memiliki bentuk yang diinginkan untuk dicetak pada benda kerja.
- Benda Kerja (Workpiece): Material yang akan diproses, yang harus bersifat konduktif listrik.
- Cairan Dielektrik: Elektroda dan benda kerja terendam dalam cairan dielektrik (seperti minyak tanah atau air deionisasi) yang berfungsi sebagai isolator dan media pendingin, serta membantu membuang partikel material yang terkikis.
- Pembangkit Pulsa Daya: Memberikan pulsa tegangan tinggi sesaat antara elektroda dan benda kerja.
Mekanisme Pemindahan Material:
- Celah (Gap): Ada celah kecil yang dikontrol secara presisi antara elektroda dan benda kerja.
- Ionization Dielektrik: Ketika tegangan diterapkan melintasi celah, cairan dielektrik akan terionisasi pada titik terdekat antara elektroda dan benda kerja, menciptakan saluran konduktif.
- Percikan Listrik (Discharge/Spark): Arus listrik mengalir melalui saluran terionisasi ini, menghasilkan percikan listrik yang sangat panas dan terlokalisasi (plasma channel).
- Peleburan dan Penguapan: Panas ekstrem dari percikan ini (mencapai ribuan derajat Celsius) melebur dan menguapkan sejumlah kecil material dari permukaan benda kerja dan juga dari elektroda.
- Pelepasan Material: Setelah pulsa listrik berakhir, saluran plasma runtuh, dan cairan dielektrik mengalir ke dalam celah, membilas partikel material yang terkikis (disebut debris) dari area kerja.
- Siklus Berulang: Proses ini berulang jutaan kali per detik, menghilangkan material sedikit demi sedikit hingga bentuk yang diinginkan tercapai.
2. Keunggulan EDM untuk Material Keras
EDM sangat diunggulkan dalam pemrosesan material keras karena beberapa alasan:
- Tidak Terpengaruh Kekerasan Material: Ini adalah keuntungan terbesar. EDM menghilangkan material melalui erosi termal, bukan pemotongan mekanis. Oleh karena itu, kekerasan material benda kerja (seperti baja perkakas yang telah dikeraskan, carbide, superalloys, atau komposit matrik) tidak menjadi penghalang.
- Mampu Membentuk Geometri Kompleks: EDM dapat membuat bentuk yang sangat rumit, rongga internal, sudut tajam, alur sempit, dan lubang kecil dengan presisi tinggi yang sulit atau tidak mungkin dicapai dengan metode permesinan konvensional.
- Tidak Ada Gaya Mekanis/Kontak Fisik: Karena tidak ada kontak fisik antara elektroda dan benda kerja, tidak ada gaya pemotongan yang diterapkan. Ini berarti tidak ada distorsi, tegangan sisa (residual stress), atau burr pada benda kerja, menjadikannya ideal untuk komponen yang tipis, rapuh, atau sangat presisi.
- Kualitas Permukaan yang Baik: EDM dapat menghasilkan kualitas permukaan yang sangat halus. Dengan menyesuaikan parameter (misalnya, mengurangi energi pulsa), finishing permukaan dapat ditingkatkan.
- Toleransi Ketat: Mampu mencapai toleransi dimensi yang sangat ketat, seringkali hingga mikrometer, yang sangat penting untuk cetakan, perkakas, dan komponen presisi.
- Memproses Material Konduktif Eksotis: Selain material keras, EDM juga mampu memproses material konduktif lainnya yang sulit diolah, seperti titanium atau exotic alloys.
3. Jenis-Jenis EDM
Ada beberapa jenis EDM yang umum digunakan, masing-masing dengan aplikasi spesifik:
- Die-Sinking EDM (Sinker EDM / Ram EDM): Menggunakan elektroda padat (biasanya grafit atau tembaga) yang berbentuk terbalik dari fitur yang ingin dibuat. Elektroda ini "ditenggelamkan" ke dalam benda kerja untuk menciptakan rongga atau cavity. Ideal untuk membuat cetakan, dies, dan tooling.
- Wire EDM (Wire-Cut EDM): Menggunakan kawat tipis (seringkali kuningan) sebagai elektroda yang bergerak terus-menerus. Kawat tersebut memotong kontur 2D yang rumit melalui benda kerja yang tebal. Mirip dengan gergaji pita, tetapi tanpa kontak fisik. Umum untuk membuat punch, die plates, dan komponen kompleks.
- Hole Drilling EDM (Fast Hole Drilling EDM): Dirancang khusus untuk membuat lubang kecil yang sangat presisi dan dalam pada material keras atau sulit, seringkali digunakan untuk lubang pendingin pada bilah turbin.
4. Tantangan dalam Pemanfaatan EDM
Meskipun banyak kelebihannya, EDM juga memiliki beberapa keterbatasan:
- Laju Penghilangan Material (Material Removal Rate - MRR) yang Lambat: Dibandingkan dengan permesinan konvensional, MRR EDM cenderung lebih rendah, terutama saat menginginkan kualitas permukaan yang sangat halus.
- Hanya untuk Material Konduktif: Benda kerja harus bersifat konduktif listrik agar proses dapat berlangsung. Ini membatasi penggunaan EDM pada material isolator.
- Keausan Elektroda: Elektroda juga terkikis selama proses (disebut tool wear), meskipun dengan laju yang lebih rendah dari benda kerja. Ini perlu dipertimbangkan dalam desain elektroda dan strategi pemesinan.
- Biaya Operasional: Konsumsi daya listrik yang tinggi dan biaya elektroda (terutama untuk desain yang kompleks) dapat meningkatkan biaya operasional.
- Cairan Dielektrik: Pengelolaan dan pembersihan cairan dielektrik serta partikel debris menjadi bagian penting dari proses.
- Zona Pengaruh Panas (Heat Affected Zone - HAZ): Meskipun minim distorsi, panas dari percikan listrik dapat menciptakan HAZ dangkal pada permukaan benda kerja, yang dapat sedikit mengubah sifat material pada lapisan paling atas.
5. Aplikasi Utama EDM untuk Material Keras
EDM adalah tulang punggung dalam produksi komponen presisi di berbagai industri:
- Pembuatan Cetakan dan Die (Mold & Die Making): Industri terbesar pengguna EDM. Digunakan untuk membuat cetakan injeksi plastik, die-casting, forging dies, dan stamping dies yang terbuat dari baja perkakas yang sangat keras.
- Produksi Perkakas (Tooling): Pembuatan perkakas pemotong, jigs, dan fixtures yang membutuhkan bentuk dan akurasi tinggi.
- Industri Dirgantara: Komponen turbin, nozzle, bagian mesin jet dari superalloys atau material tahan panas.
- Medis: Pembuatan instrumen bedah presisi, implan kecil, atau komponen untuk perangkat medis.
- Otomotif: Komponen powertrain, valve seats, atau cetakan untuk komponen mesin.
- Elektronik: Memproduksi komponen mikro atau micro-electro-mechanical systems (MEMS).
Dengan kemampuannya yang unik untuk memproses material yang sangat keras dan membentuk geometri kompleks tanpa kontak fisik, EDM telah menjadi proses manufaktur yang tak tergantikan dalam industri modern yang menuntut presisi dan inovasi.
0 Komentar
Artikel Terkait
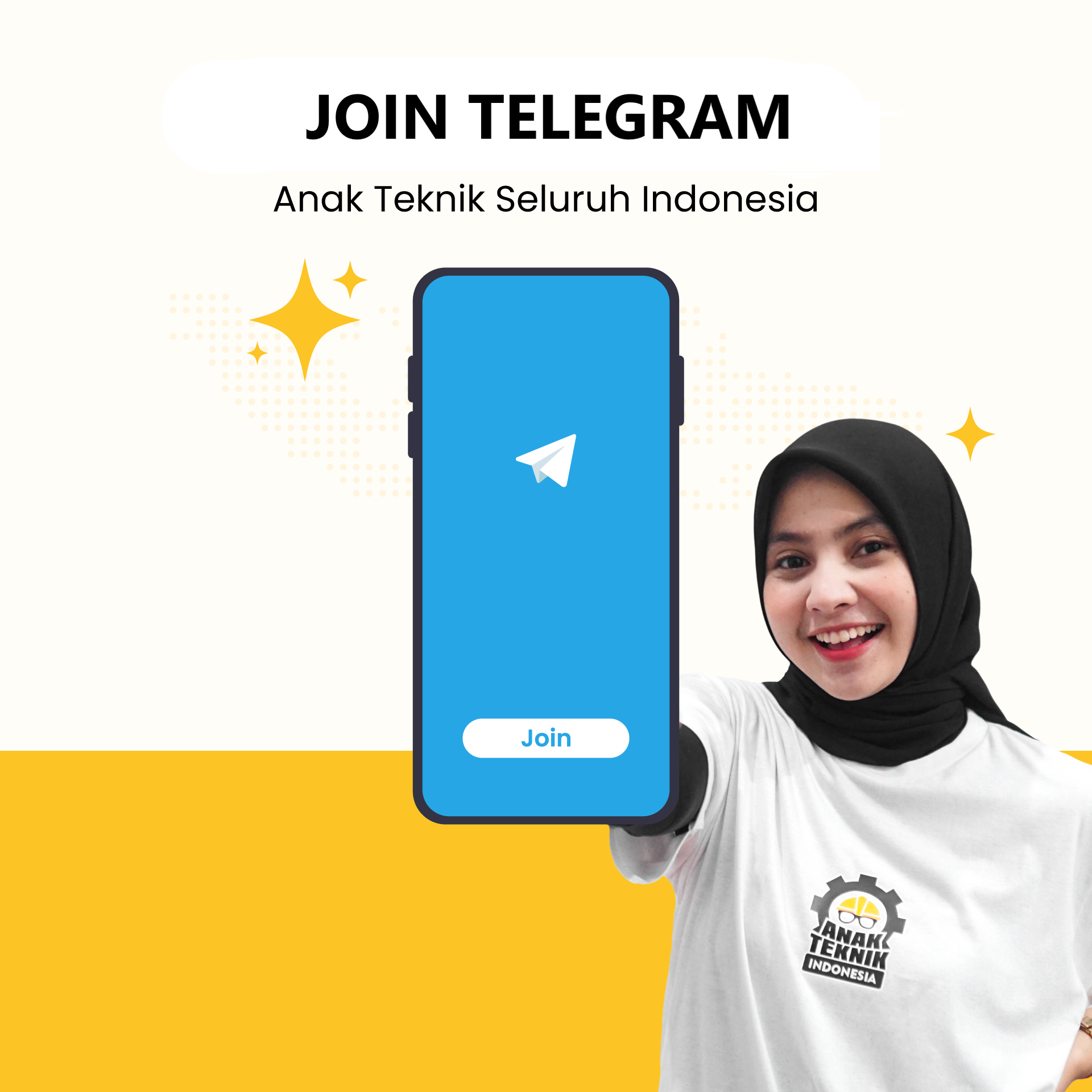